Pumbaa 66 / 123kW電気用セントラルE軸4.5T-6.0Tロジスティクス車両 / 6Mバス
Pumbaa PMEA5300ZCENTRAL E-Axle技術パラメーター
定格車軸荷重(kg) |
3500 |
車軸ハウジング形成方法 |
スタンピングと溶接 |
ハウジング断面(mm) |
105×105×6 |
最高速度(km/h) |
100 |
削減比 |
16.6 |
ノミネート/ピーク出力トルク(nm) |
135/320 |
定格/ピークパワー(KW) |
66/123 |
最高速度(rpm) |
12000 |
運動寸法(mm) |
φ275×280 |
リーフスプリング取り付け距離(mm) |
952 |
リム取り付け距離(mm) |
1555 |
全体幅(mm) |
1757 |
ブレーキ仕様(エアブレーキ) |
ドラムポーズ:φ310×100 |
最大ブレーキトルク(0.6mpa) |
2×5200NM |
ホイールボルト仕様 |
12-M22×1.5 |
ホイールボルト分布サークル直径(mm) |
φ222.25 |
ストップ(mm)を見つける |
φ160.8 |
アセンブリ重量 (kg) |
310 |
description2
電気駆動車軸の主要な技術:軽量。高い信頼性。高性能材料
電気車両とハイブリッド車両の台頭により、より効率的で環境に優しい輸送モードを実現するために、頑丈なトラックセクターで電気車軸技術も徐々に導入されています。ただし、重いトラックの統合された電気車軸の重量は1トンに近いため、快適さとハンドリングの安定性に新たな課題があります。したがって、軽量は重いトラックの電気車軸技術の重要な問題になっています。
環境保護に対する意識が高まり、燃費の要件が増えているため、電気車両とハイブリッド車の市場需要が高まっています。商業輸送の分野の主力として、頑丈なトラックはこの傾向に従い、より高度な電力技術を導入する必要があります。重いトラックのパワートレインのコアコンポーネントとして、電気車軸の重量と性能は、重いトラックの全体的な性能に不可欠です。したがって、軽量技術は、重いトラック用の統合電気車軸の開発において重要な問題となっています。
軽量設計:軽量のデザインは、頑丈なトラック電気駆動車軸の軽量を実現するための基礎と鍵です。次元の最適化、形態学的最適化、構造最適化は、軽量設計の重要な手段です。寸法の最適化は、部品の強度と剛性を確保しながら、部品のサイズを小さくすることにより体重を減らします。地形の最適化は、部品の形状とプロファイルを変更することにより、部品の軽量化効果を改善します。構造の最適化により、部品の構造とレイアウトを最適化することにより、重量が減少します。これらの設計方法は、コンピューター支援設計やシミュレーション分析などのツールの助けを借りて実装する必要があります。
軽量材料:軽量の材料は、大量のトラックのための電気車軸の軽量で重要な役割を果たします。一般的に使用される軽量材料には、高強度鋼、アルミニウム合金、マグネシウム合金、非金属材料、複合材料が含まれます。高強度鋼は、強度を犠牲にすることなく、部品の厚さと重量を減らすことができます。アルミニウム合金とマグネシウム合金は、密度が低く、処理特性が良好であり、軽量と高強度の部品を作るために使用できます。プラスチックや繊維強化複合材などの非金属材料は、密度が低く、良好な包括的な特性を持ち、いくつかの非構造部品の製造に適しています。
軽量製造:軽量製造は、大型トラック電気駆動車軸の軽量を実現するための重要なリンクです。熱成形、レーザーテーラード溶接、ロール形成、ハイドロフォーミングなどの新しい製造プロセスにより、複雑な形の部品の効率的な製造と軽量化が可能になります。熱成形プロセスを使用して、加熱と形成により部品の形状を複雑にし、明るくすることができます。テーラードレーザー溶接は、複数の部品を正確に結合することができ、使用される溶接材料の量と部品の重量を減らすことができます。ロールの形成とヒドロフォーミングは、連続的な形成により大規模で高強度の部分を生成し、溶接接合部の使用を減らすことができます。
軽量とコスト管理のバランス:軽量の程度は、材料コスト、生産コスト、パフォーマンス要件を包括的に検討する必要があります。重量の減少に加えて、重積のトラック電子アクスルの安全性、NVH(騒音、振動、剛性)の性能と耐久性を確保することも必要です。その結果、軽量設計、軽量材料、軽量製造には、コストとパフォーマンスの間に合理的なトレードオフが必要です。ヘビーデューティトラックの電子軸の最適なパフォーマンスは、最小限のコスト、体重、プロセス投資でのみ達成できます。
電気駆動車軸の主要な技術 - 高い信頼性
信頼性の作業に関しては、ユーザーの使用データに基づいて電気車軸の耐久性条件を定義する必要があります。ユーザーの実際の使用条件と操作条件に関するデータを収集することにより、さまざまな条件下で電子アクスルの動作状態をよりよく理解し、それに応じて耐久性条件を定義することができます。これにより、電子アクスルの構造設計を最適化し、車両アセンブリの持久力ロードテスト中にその信頼性を保証します。
第二に、高い統合によってもたらされる多様なテストコンテンツの設計統合の課題を満たすために、電子制御、モーター、ギアボックス、車軸などの複数の側面を包括的に検討する必要があります。高レベルの統合により、これらのコンポーネントは密接に結合し、それらの間の影響と結合はより複雑になります。したがって、さまざまな動作条件下での電子軸のパフォーマンスと信頼性を包括的に評価するために、包括的な一連のテストを設計する必要があります。
さらに、ディーププラットフォームの設計は、電子アクスルの信頼性を向上させるための鍵の1つでもあります。電子軸の使用の要件は車両ごとに異なる場合があるため、設計プロセス中にこの複合使用ニーズの互換性を考慮する必要があります。統一されたプラットフォーム設計スキームを採用することにより、さまざまなモデルのニーズをより適切に満たし、電気駆動車軸の汎用性と信頼性を改善できます。
電気駆動車軸の主要な技術 - 高性能材料
電気車軸では、高性能材料の需要も増加しており、高速、高温および高温ベアリング、長寿命の高断熱磁石ワイヤ、高性能シリコン鋼シートなどの主要な技術と材料が重要な役割を果たします。
高速および高電圧電気自動車モーターの開発により、ベアリングは、モーターの作業プロセス中の摩耗やシャフト電流腐食などの問題に直面しています。これらの問題を解決するには、ベアリングは高速、高断熱、高温抵抗を持つ必要があります。これを達成するには、高強度のリテーナー技術や断熱技術などの重要な問題に焦点を当てる必要があります。
高強度のリテーナー技術に関する研究は、負荷をかける容量とベアリングの防止性能を改善することを目的としています。高速モーターのニーズを満たすために、リテーナーの構造設計と材料選択を最適化することにより、ベアリングの強度と耐摩耗性を改善できます。
断熱技術の研究は、ベアリングの断熱性能を改善し、シャフト電流腐食の問題の発生を防ぐことを目的としています。電気駆動システムでは、モーターが動作しているときに生成された電磁界により、ベアリングは電流のチャネルになり、シャフト電流腐食が発生する可能性があります。したがって、ベアリングの絶縁能力を改善し、シャフト電流腐食からそれらを保護するために、高度に断熱材と断熱技術を探す必要があります。
電気駆動車軸の主要な技術 - 軽量
環境保護に対する意識が高まり、燃費の要件が増えているため、電気車両とハイブリッド車の市場需要が高まっています。商業輸送の分野の主力として、頑丈なトラックはこの傾向に従い、より高度な電力技術を導入する必要があります。重いトラックのパワートレインのコアコンポーネントとして、電気車軸の重量と性能は、重いトラックの全体的な性能に不可欠です。したがって、軽量技術は、重いトラック用の統合電気車軸の開発において重要な問題となっています。
軽量設計:軽量のデザインは、頑丈なトラック電気駆動車軸の軽量を実現するための基礎と鍵です。次元の最適化、形態学的最適化、構造最適化は、軽量設計の重要な手段です。寸法の最適化は、部品の強度と剛性を確保しながら、部品のサイズを小さくすることにより体重を減らします。地形の最適化は、部品の形状とプロファイルを変更することにより、部品の軽量化効果を改善します。構造の最適化により、部品の構造とレイアウトを最適化することにより、重量が減少します。これらの設計方法は、コンピューター支援設計やシミュレーション分析などのツールの助けを借りて実装する必要があります。
軽量材料:軽量の材料は、大量のトラックのための電気車軸の軽量で重要な役割を果たします。一般的に使用される軽量材料には、高強度鋼、アルミニウム合金、マグネシウム合金、非金属材料、複合材料が含まれます。高強度鋼は、強度を犠牲にすることなく、部品の厚さと重量を減らすことができます。アルミニウム合金とマグネシウム合金は、密度が低く、処理特性が良好であり、軽量と高強度の部品を作るために使用できます。プラスチックや繊維強化複合材などの非金属材料は、密度が低く、良好な包括的な特性を持ち、いくつかの非構造部品の製造に適しています。
軽量製造:軽量製造は、大型トラック電気駆動車軸の軽量を実現するための重要なリンクです。熱成形、レーザーテーラード溶接、ロール形成、ハイドロフォーミングなどの新しい製造プロセスにより、複雑な形の部品の効率的な製造と軽量化が可能になります。熱成形プロセスを使用して、加熱と形成により部品の形状を複雑にし、明るくすることができます。テーラードレーザー溶接は、複数の部品を正確に結合することができ、使用される溶接材料の量と部品の重量を減らすことができます。ロールの形成とヒドロフォーミングは、連続的な形成により大規模で高強度の部分を生成し、溶接接合部の使用を減らすことができます。
軽量とコスト管理のバランス:軽量の程度は、材料コスト、生産コスト、パフォーマンス要件を包括的に検討する必要があります。重量の減少に加えて、重積のトラック電子アクスルの安全性、NVH(騒音、振動、剛性)の性能と耐久性を確保することも必要です。その結果、軽量設計、軽量材料、軽量製造には、コストとパフォーマンスの間に合理的なトレードオフが必要です。ヘビーデューティトラックの電子軸の最適なパフォーマンスは、最小限のコスト、体重、プロセス投資でのみ達成できます。
要約すると、電気車軸の主要な技術における軽量、高解放性、高性能材料が、電気自動車の開発において重要な役割を果たしてきました。高速、高断熱、高温ベアリング、長寿命の高断熱磁石ワイヤ、高性能シリコンスチールシートなどの主要な技術と材料を研究することにより、電気駆動システムの性能と信頼性を改善し、電気自動車技術のさらなる開発を促進することができます。将来的には、Pumbaaは、高性能材料の品質と効率を改善するために、研究と革新を継続的に強化し、電気自動車産業の持続可能な開発に貢献する必要があります。
メッセージを残す
ブログ
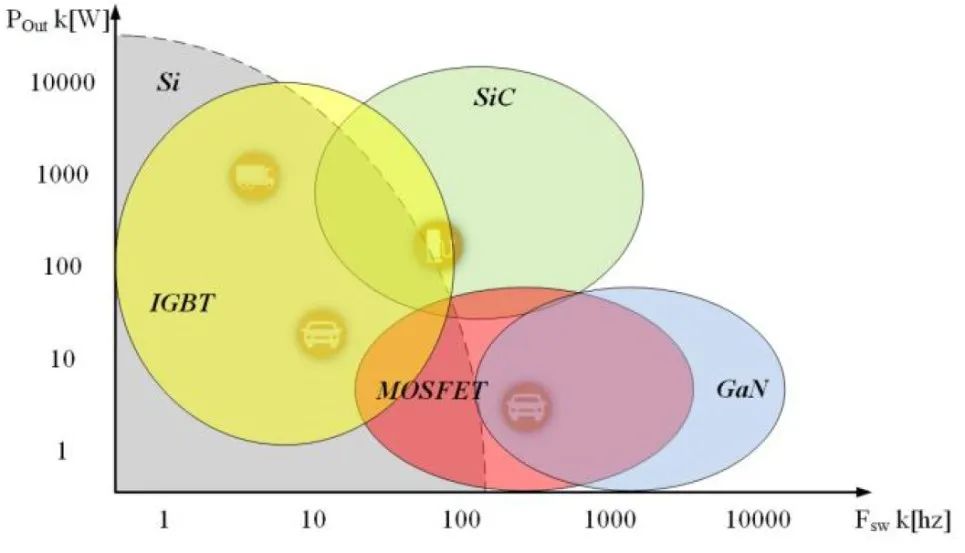
SIC+SI混合炭素融合インバーター・概念からシステムソリューションの実装へのパノラマ分析
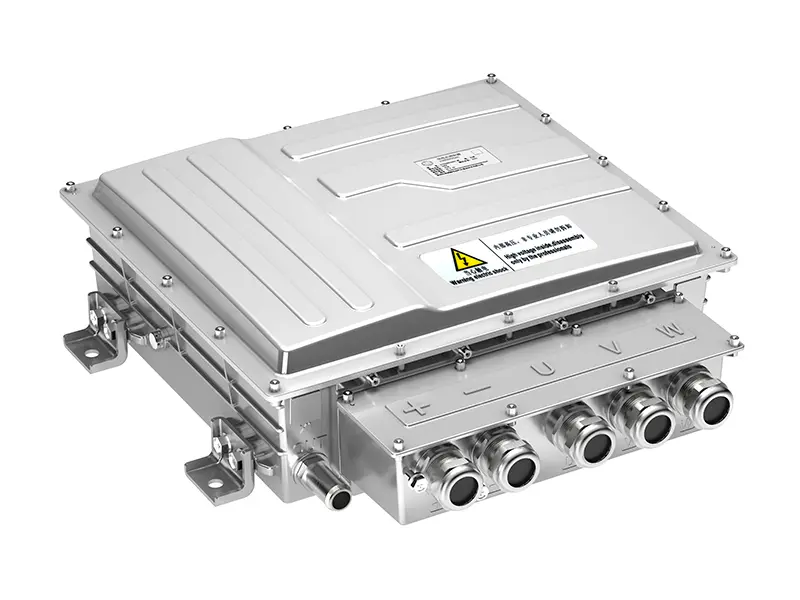
電気自動車モーターの主要なコンポーネントと利点の調査
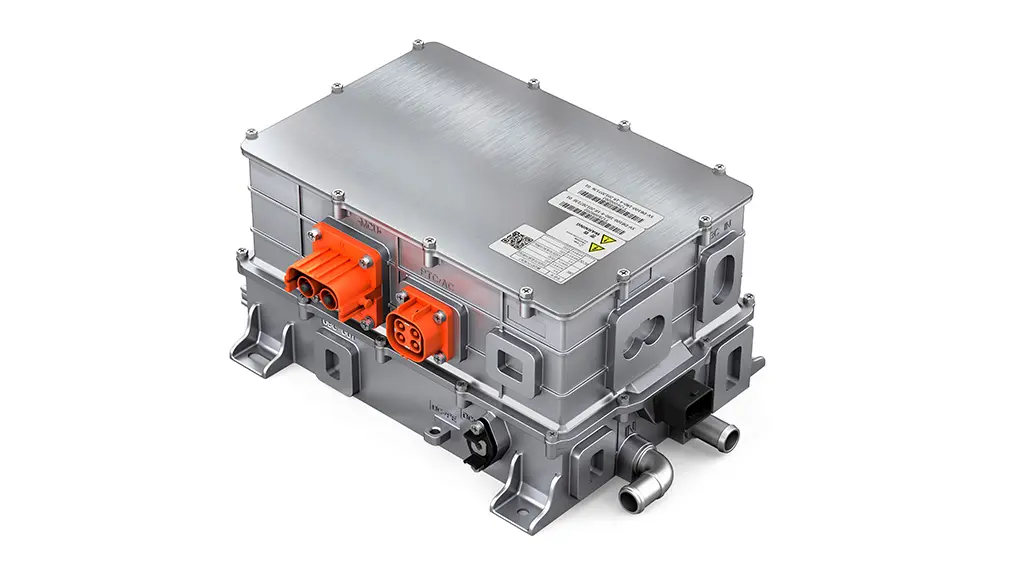